To use slides to create undercut shapes in your molds, you need to determine how you’ll actuate the slides to move them through the mold itself. Foundries frequently find themselves choosing between two methods: some form of mechanical actuation and hydraulic cylinders. For the purposes of this article, we are going to consider horn pins for the mechanical actuation.
While these two perform essentially the same action, there are different situations where it makes sense to use one instead of the other. Generally, factors like your budget and your foundry’s preference play into a design engineer’s decision on which to use.
But more specifically, the casting complexity and the physical machine interface make a crucial difference.
Let’s take a closer look.
First off — what is the difference between the two?
Horn pins — also called cam pins, actuator pins, or angle pins — perform a straightforward mechanical movement in your mold. With the help of a slide block, these pins move a slide in and out to create an undercut in a way that still allows you to eject the casting once it’s completed. This type of “old technology” is generally less expensive than hydraulic cylinders, more durable, and easier to maintain.
Hydraulic cylinders perform the same action but with hydraulic pressure instead of with a purely mechanical operation. The cylinder pushes a slide in before the molten metal is poured and pulls it back out before the casting is extracted. With hydraulic cylinders, there is more equipment involved, including the hydraulic pump, the cylinder and the connection lines, as well as the actual slides themselves. This can make maintenance more expensive, but hydraulic systems are able to apply much greater force and allow for much longer stroke lengths as well as having parts that are fairly standard and easy to replace.
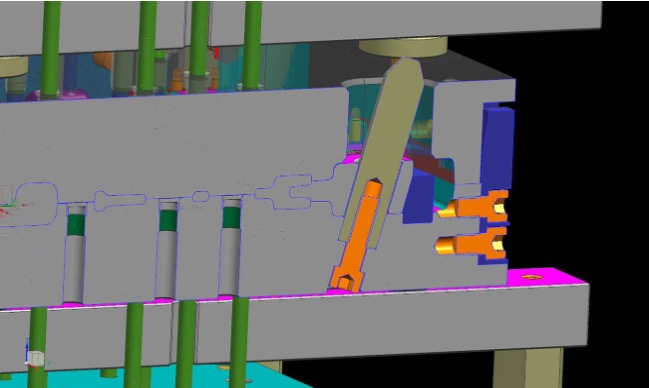
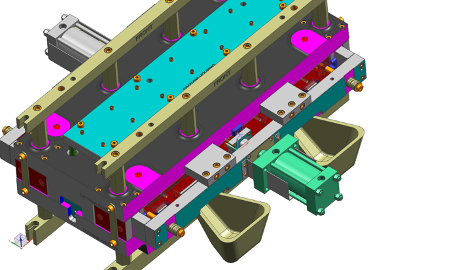
In addition to budget, your foundry’s capabilities and preferences are also important factors to consider while designing. For example, if your foundry isn’t equipped to use hydraulic cylinders because you’ve always used horn pins, your tooling partner should accommodate for that.
Casting shape, size, and complexity
As a general rule, any time you add complexity to a mold or tooling, there’s more room for error. This means when your casting shape allows for small, easy movements that don’t require pins or slides to travel very far, it makes sense to use horn pins. In those situations, hydraulic cylinders are overkill.
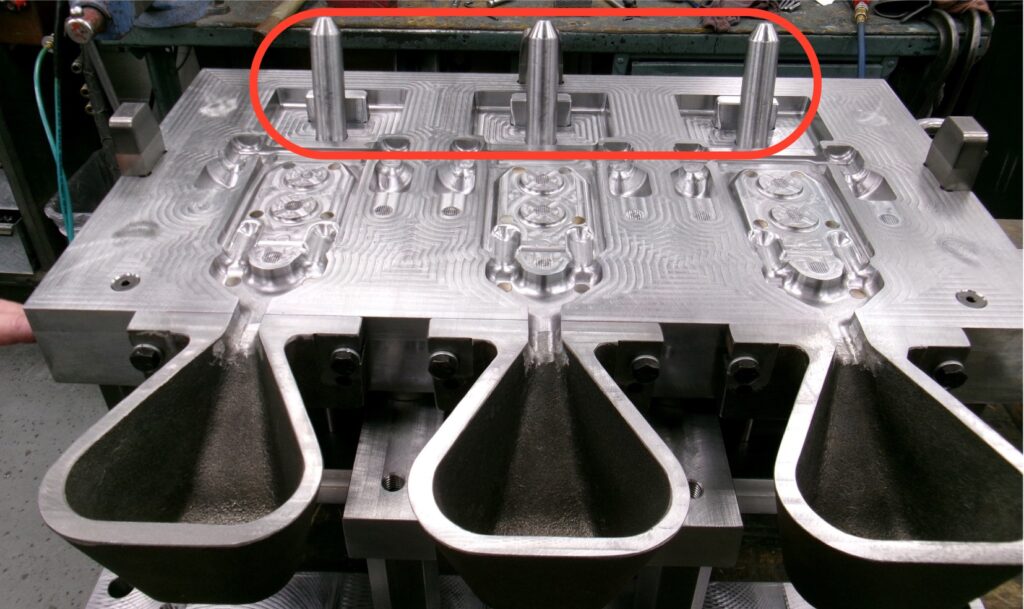
But once the pins have a larger distance to cover, the pins themselves must be longer. And when the pins are longer, the mold needs to be able to open more to allow for this movement because it’s the mechanical opening and closing motion that actually moves the pins that actuate the slides.
In contrast, hydraulic cylinders move slides horizontally, which does not require the mold to open more to accommodate for longer pins or rods. While this does necessitate more space around the mold, it is still simpler and more effective to use hydraulic cylinders for longer slide movements.
Hydraulic cylinders are also the superior option for large areas of undercut shape. Horn pins are a mechanical component; if the weight and size of the slide are too big, they don’t have enough force behind them to move the slides properly and will likely wear faster.
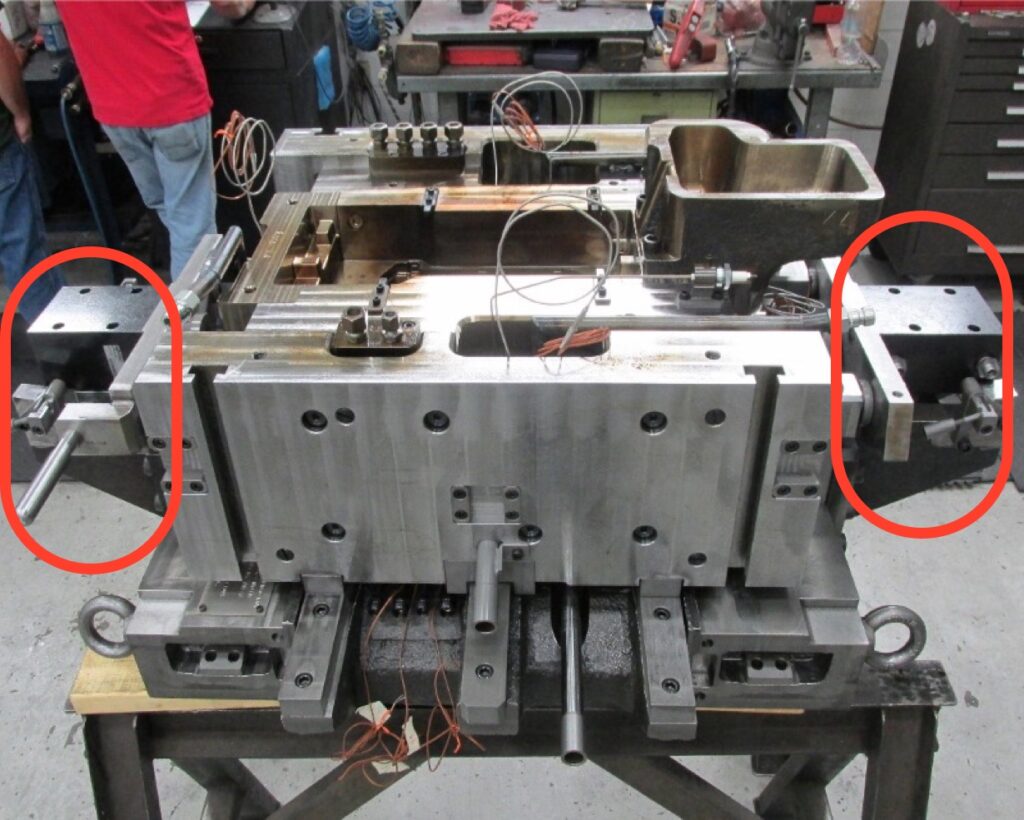
This is also true for complex castings. If you need multiple slides, your slides have a long distance to travel within the mold, or you need additional cooling strategies, hydraulic cylinders are the better option. Not only can you have a longer stroke or taller slide, but hydraulic cylinders are more exposed than horn pins, meaning they can be used as part of the cooling strategy. On the other hand, horn pins muddle the internal design in situations like these, adding unnecessary complexity that can make maintenance and trouble-shooting difficult.
Physical machine interface
With both horn pins and hydraulic cylinders, there needs to be room for movement. As we mentioned above, longer horn pins require the mold to open more so there’s space to remove the pin. Similarly, when planning for a design with hydraulic cylinders, it’s crucial to consider your stroke.
For example, if you have an undercut feature that’s 3 inches long, your hydraulically powered slide may need to move 4 inches to have enough clearance once removed. So, if you have a 4-inch rod, the cylinder behind it also needs to be at least that long. This gives you 8 to 10 inches that must be accounted for in your design.
Additionally, foundry tooling with hydraulic cylinders needs to be more accessible than those with horn pins. Not only do you need to maintain the equipment itself, but you must also maintain the lines and hook ups you need for the hydraulic pump. This means more space.
Experience makes the difference
Ultimately, the decision whether to use horn pins or hydraulic cylinders comes down to what’s best for your mold, your core box, and your foundry. For expert guidance, get in touch with our team of design engineers. We’ll figure out your needs and create a long-lasting tooling solution together.