Nothing is more frustrating than receiving your foundry mold, pouring your first part, and having that piece come out wrong. The downtime, the delays, the expense, the hassle — it’s a pain.
Your finished part should come out perfectly from the first pour and every pour after.
When your foundry works with Anderson Global, we collaborate with you to ensure your new mold meets all your expectations. You bring your goals and foundry-specific knowledge, we’ll bring our cross-industry best practices and expertise. Together we’ll build a high-quality, long lasting solution.
While there’s no run-of-the-mill project, each one follows the same design process.
- Request a quote
- Design for manufacture, simulations, casting process design, and tooling design
- Building your mold
- Support and service
- Custom foundry mold solutions for your custom needs
Here’s what you need to know.
The beginning: requesting a quote and setting expectations
When you reach out for a quote, our team will often request more information before we get started. The more details you give us about your goals, expectations, and processes, the quicker and smoother this beginning phase will go.
Your capabilities and expectations
Our design team will sit down with yours for a technical meeting where we’ll discuss your foundry’s capabilities and the expectations for your foundry mold.
Some common considerations and questions include:
- What material will the final casting be made of?
- What material will the mold be made of?
- What type of equipment is at your foundry?
- What process (tilt pour, gravity pour, etc.) do you run at your foundry?
- What are your foundry’s conditions? For example, what cooling options do you have available?
- What industry-specific requirements and standards do we need to adhere to?
- What type of surface finish will your casting need?
Determining the answers to these questions and generating a quote can take anywhere from a day to a week. It depends on the complexity of the project, what additional components your design needs, what you’re able to show us at the start (like a 3D casting model, 2D blueprints, or a finished machined part), and your level of collaboration.
From there, our team will clarify lead times, send you a quote and remain available to further refine the quote as needed or answer any questions.
Better designs and simulations lead to better molds
In the design process, there are three phases: design for manufacture (DFM) and casting simulations, casting process design, and tooling design.
Let’s look at each one.
Phase one: DFM and casting simulations
For this first phase, we build on the questions and considerations from the quoting stage as we analyze the part and the casting models for manufacturing purposes. In other words, how castable is it? Can the part be manufactured the way it’s been designed? And most importantly, can it be made in regular production with a robust process?
This is where knowledge of the foundry’s practices and capabilities becomes vital. Based on what your foundry and team can do, as well as the purpose of the final product, sometimes we tweak the design a little, and sometimes we redo it significantly. All, of course, in collaboration with your team.
Designing a process and tooling around a casting model, only to find out that casting design needs to change, would be a huge waste of time and resources. Creating casting simulations helps negate this. Often happening in parallel with DFM, these simulations identify potential issues and inefficiencies in the casting design, the gating, and risers. Simulations are an important step that can shorten lead time and ultimately reduce the total cost.

We use EKK to run simulations, but the tool is only as good as the person using it. Our team has spent thousands of hours observing how the software interprets settings like metal temperature and how foundry conditions impact the simulation. Simply put, they’ve seen it all — and are well-equipped to analyze results in real time and learn from each run.
Our simulation analysts work closely with the design engineering team and your foundry to ensure the simulation is as good as it can be before moving on to the next phase.
Phase two: Casting process design
Next comes the process design. This phase takes the casting shape into consideration, the type of casting process to be used, as well as any core requirements, options for the location of the parting lines, and how we’ll split up the tool for manufacturing purposes.
Phase three: Tooling design
Next is the tooling design. We design the mold, taking into account the need for cores or sliders, available cooling options, your design standards and our own manufacturing standards. Depending on your preference, we can collaborate extensively or take your input and run with it.
Anderson Global has an extensive library of standardized, fully field-tested mold subcomponents that allows our design process to move quickly and efficiently. We’ve built this Siemens NX library on decades of experience. It contains thousands of parts, designs and learnings that we pull from when creating your mold.
Once we’ve gathered the standard components we need and designed any non-standard parts, we build 3D models in our software. These models enable our internal departments to talk to each other using a single source of data. When the whole team understands the designer’s intent, the manufacturing team can build the mold consistently, reliably and easily.
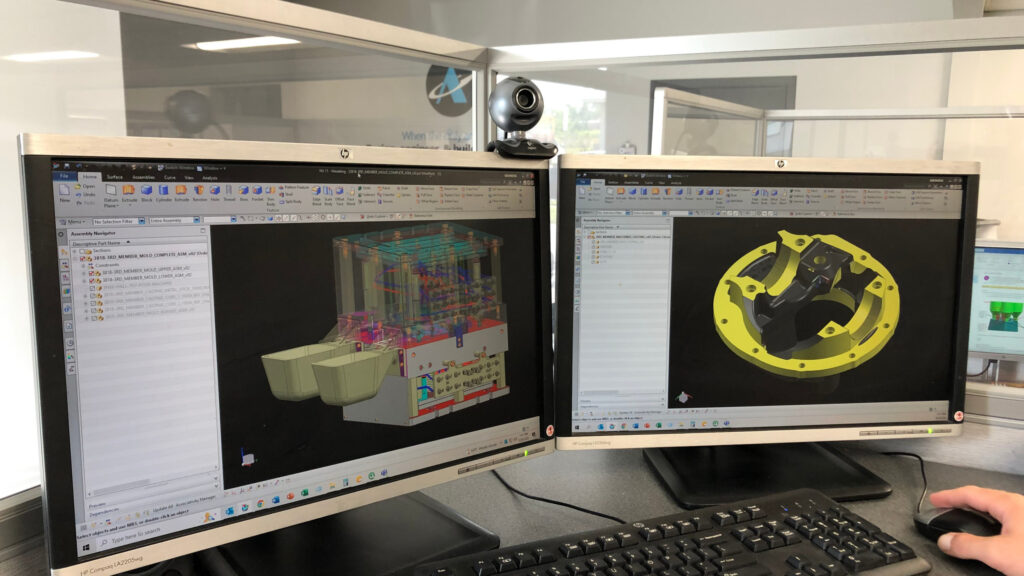
As part of this process, Anderson Global designers produce a detailed 3D model that contains all attributes and features required to build the tool, including an embedded bill of materials. This model makes any future repairs or spare parts orders simple and efficient.
Building your foundry mold
After the design phase, it’s time to cut the metal.
Our project leaders purchase the materials and draft specific instructions. NC programmers write the CNC programs. Then everything heads to the shop floor.
There, the CNC machine operators manufacture your foundry mold components before sending them on to our bench area for final details, finishing, and assembly.
This is where our journeyman patternmakers carefully review and assemble each mold component for fit and function. At this moment in particular, skill and experience are everything. We work with the best because it makes the difference between a passable mold and a world-class, foundry-friendly mold.
But the process doesn’t end there.
Finishes and fine-tuning at your foundry
While our goal is for your finished part to come out perfect from the first pour, that doesn’t always happen. If the part doesn’t meet your expectations for any reason, our team will work with you until it does.
Because of our exposure to the greater foundry world, our team has insight into best practices across industries. This open-minded approach enables us to try different strategies to troubleshoot your foundry mold for a finished part that is exactly what you expected.
There’s no such thing as a run-of-the-mill casting mold
Building a new foundry mold is a creative and collaborative process. There are multiple ways to get to the end result, and our job is to find the most cost-effective, most reliable, and longest lasting one for your foundry.
At Anderson Global, we have a lot of foundry experience, but we don’t know your foundry like you do. Conditions like your employees’ experience levels, your furnace conditions, your available cooling methods and even your physical location all impact the final mold.
The best way to build casting molds is by working together and learning from each other. Let’s get started.